ISO 9001 Audit Guide | Genveritas Technologies
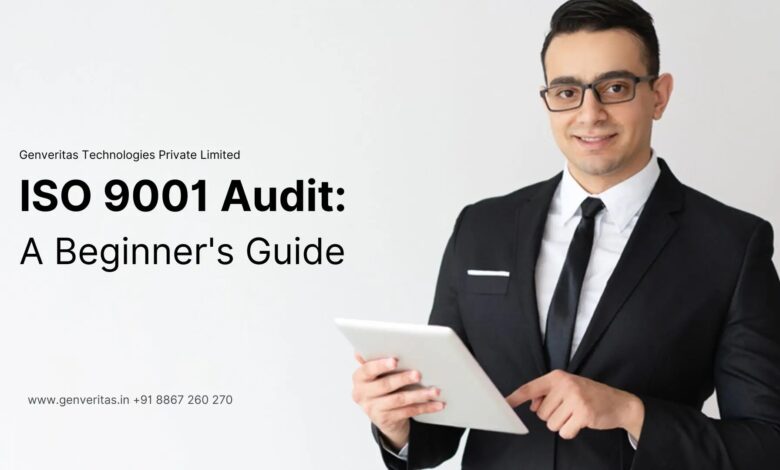
Understanding ISO 9001
ISO 9001 is a globally recognized standard that outlines the requirements for a quality management system (QMS). It provides a framework for organizations to ensure consistent quality in their products and services. An ISO 9001 audit is a systematic examination of an organization’s QMS to assess its compliance with the standard.
Types of ISO 9001 Audits
- Internal Audit: A manufacturing company might conduct an internal audit to assess if its production processes are adhering to the ISO 9001 requirements for quality control and documentation.
- Supplier Audit: A technology firm might audit its component suppliers to ensure they meet the quality standards required for their products.
- Certification Audit: A healthcare provider might undergo a certification audit to demonstrate to patients and regulators that their services meet international quality standards.
The Audit Process
- Planning: An audit team might develop a plan to assess a software development company’s QMS, focusing on areas like project management, change control, and customer satisfaction.
- Document Review: The team would review the company’s quality manual, procedures, and records to ensure they are comprehensive and up-to-date.
- Interviews: They might interview project managers, developers, and quality assurance personnel to understand their roles in the QMS and gather feedback on its effectiveness.
- Observations: The team might observe the development process, including code reviews, testing, and defect tracking, to assess compliance with defined procedures.
- Findings: Any non-conformities or areas for improvement would be documented, such as a lack of clear customer satisfaction metrics or inconsistent project documentation.
- Closing Meeting: The audit team would present their findings to the company’s management, discussing corrective actions and potential areas for improvement.
Benefits of ISO 9001 Certification
- Enhanced Customer Satisfaction: A manufacturing company with ISO 9001 certification can demonstrate to customers that their products are produced using consistent quality standards.
- Increased Efficiency: A software development company can streamline its processes and reduce rework by implementing a QMS that emphasizes continuous improvement.
- Improved Market Access: Government contracts or partnerships with multinational corporations often require ISO 9001 certification.
- Enhanced Reputation: A healthcare provider can build trust with patients by demonstrating its commitment to quality through ISO 9001 certification.
Preparing for an ISO 9001 Audit
- Review and Update Documentation: A manufacturing company might update its quality manual to reflect changes in production processes or regulatory requirements.
- Train Employees: A software development company can provide training to employees on the QMS, including their roles and responsibilities.
- Conduct Internal Audits: A healthcare provider can conduct regular internal audits to identify and address non-conformities before a certification audit.
- Implement Corrective Actions: If an internal audit reveals issues, a company can implement corrective actions, such as improving training or updating procedures.
By understanding the basics of ISO 9001 audits and preparing adequately, organizations can ensure a successful audit process and reap the benefits of certification.
Tags: #ISO 9001, #Quality Management System (QMS), #Audit, #Certification, #Quality Control, #Quality Assurance, #Internal Audit, #Supplier Audit, #Certification Audit, #ISO 9001 Standards, #ISO 9001 Requirements, #Audit Preparation, #Audit Process, #Audit Findings, #Corrective Actions, #Quality Improvement, #Manufacturing, #Healthcare, #Software Development, #Automotive, #Aerospace, #Education